Electromagnetic interference (EMI) and radio frequency interference (RFI) can significantly disrupt modern electronics. EMI line filters have a vital function in reducing these disturbances, guaranteeing the uninterrupted operation of devices across numerous applications. This article delves into the nuances of EMI line filters, focusing on ferrite core materials based on publicly available technical research.
Understanding EMI and RFI
EMI and RFI are types of unwanted signals that can affect electronic devices. EMI includes all kinds of electromagnetic emissions, while RFI specifically refers to interference in the radio frequency range (10 kHz to 1 GHz). Distinguishing between these types of interference is essential for designing effective suppression solutions.
Core Types in EMI Filters: UU, UF, UI, and UT Cores
Ferrite cores are essential for EMI filter performance, with manufacturers choosing them according to their electromagnetic properties and application demands.
- UU Cores are ideal for high-power applications due to their high magnetic flux capacity and low core loss. They provide a stable magnetic path, making them suitable for transformers and inductors where efficiency is critical.
- UF Cores: Known for their high permeability and stability at high frequencies, UF cores excel in precision high-frequency noise suppression applications.
- UI Cores: Robust and efficient, UI cores are designed for compact configurations where reliability is paramount.
- UT Cores: Offering a balance between performance and cost, UT cores are suitable for general-purpose applications.
Selecting suitable ferrite materials (MnZn, NiZn) ensures optimal core performance across specific frequency ranges and environments.
Design Considerations: Parasitic Parameters
Effective filter design must consider parasitic parameters like Equivalent Parallel Capacitance (EPC) and Equivalent Series Inductance (ESL). These parasitics can degrade filter performance by introducing unintended resonances and reducing attenuation at certain frequencies. Advanced design techniques, including precise material selection and incorporating conductive layers, help minimize these effects, ensuring optimal filter performance.
Integrated EMI Filters: Embedded Conductive Layers
The integration of conductive layers within EMI filters enhances their performance by significantly improving attenuation characteristics and reducing physical size. This technique is particularly beneficial in compact electronic devices where space is limited. Integrated filters with embedded conductive layers exhibit superior performance in high-frequency noise suppression.
Common-Mode and Differential-Mode Noise Suppression
EMI line filters are designed to address both common-mode and differential-mode noise:
- Common-Mode Noise: Characterized by its presence in-phase on both conductors, this noise is commonly mitigated with common-mode chokes and capacitors.
- Differential-Mode Noise: Appearing out of phase between conductors, this noise requires differential-mode chokes and X-capacitors.
Understanding the specific noise characteristics and operational environment is essential for selecting the appropriate filter components and configurations.
Applications of EMI Line Filters
EMI line filters are essential across various industries, including:
- Power Electronics: Ensuring the smooth operation of switching power supplies and inverters by mitigating conducted noise.
- Automotive Industry: Protecting sensitive electronic systems from noise generated by motors and other high-power components.
- Consumer Electronics: Maintaining the integrity of audio and video signals, enhancing the user experience.
Power Line Filters
Power line filters are specialized EMI filters designed to suppress noise in AC or DC power lines, protecting electronic equipment from conducted interference originating from the power supply. They incorporate inductors and capacitors to attenuate unwanted frequencies, ensuring clean power delivery to sensitive devices.
Insertion Loss in EMI Filters
Insertion loss is a critical parameter in evaluating EMI filter performance. It measures the filter’s ability to attenuate unwanted signals with the formula insertion loss :
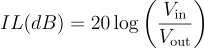
Where is the input voltage and
is the output voltage.
Effective filters exhibit high insertion loss at targeted frequencies, indicating superior noise suppression.
Electromagnetic Compatibility (EMC)
Electromagnetic Compatibility (EMC) refers to a device’s ability to function without emitting or being affected by electromagnetic interference. Achieving EMC involves designing systems that minimize emitted interference and withstand external noise, with EMI filters playing a fundamental role in ensuring EMC in electronic systems.
Passive and Active Filters
EMI filters can be passive or active:
- Passive Filters: Utilize components like resistors, inductors, and capacitors to attenuate noise. They are reliable and straightforward but may have performance limitations.
- Active Filters: Incorporate components like transistors and operational amplifiers, offering enhanced performance and greater flexibility, but are more complex and require a power source.
Checking Voltage and Spikes with Line Filters
To check voltage and spikes managed by line filters:
- Use an oscilloscope to measure the input and output waveforms.
- Place probes at the input and output terminals of the filter.
- Compare the amplitude of spikes before and after the filter to determine its effectiveness.
How to Check Leakage Inductance of Line Filter
To check the leakage inductance of a line filter, use an LCR meter or impedance analyzer. Connect the meter across the filter’s inductors and measure the inductance at the specified frequency. Compare the measured value with the filter’s specifications to ensure it meets the required performance. The formula for inductance L is:

where V is the voltage, ω is the angular frequency, and L is the current. Proper measurement of leakage inductance helps in assessing the filter’s ability to suppress high-frequency noise .
How to Calculate Load on Line Filter
Calculating the load on a line filter involves determining the total current and power that the filter will handle. Sum the current drawn by all connected devices to find the total load current. The formula for total current is:

Ensure the filter’s current rating exceeds this value to prevent overheating and ensure reliable operation. Additionally, consider the power dissipation in the filter components to ensure they can handle the thermal load without degradation .
Designing Line Filters for LED Drivers
When designing a line filter for an LED driver:
- Select suitable inductors and capacitors to suppress EMI while maintaining LED performance.
- Use common-mode chokes and differential-mode capacitors.
- Ensure the filter’s cut-off frequency is below the LED driver’s operating frequency.
- Validate the design using simulation software to optimize component values and ensure effective EMI suppression.
At Shreejee Electronics, we excel in incorporating cutting-edge research findings into our high-quality EMI line filters. We utilize latest manufacturing techniques and stringent quality control procedures to guarantee that every filter surpasses performance and reliability standards.
Contact us for our custom solutions cater to clients’ unique demands, solidifying our reputation as a trusted supplier of reliable EMI suppression.