In the transformer industry, many suppliers rely on job work — outsourcing critical production steps to third-party workshops. While this may reduce their internal costs, it can come at your expense as a customer.
What Really Happens Behind the Scenes?
In job-work-based production, key processes such as coil winding, ferrite core assembly, soldering, and varnish impregnation are carried out at disconnected, uncontrolled facilities. There is often little to no oversight on material sourcing, workmanship, or testing standards.
Here’s what this can mean for the end user:
- Use of scrap-grade ferrite cores bought from secondary markets
- Substitution of aluminum wire for copper without disclosure
- Poorly wound coils with air gaps and uneven layers
- Improper curing of insulation varnish, leading to early breakdown
- No standard testing, just visual inspection
These shortcuts often result in overheating, premature failure, inconsistent performance, and in many cases, damage to the circuits they’re integrated into.
Why In-House Manufacturing Matters
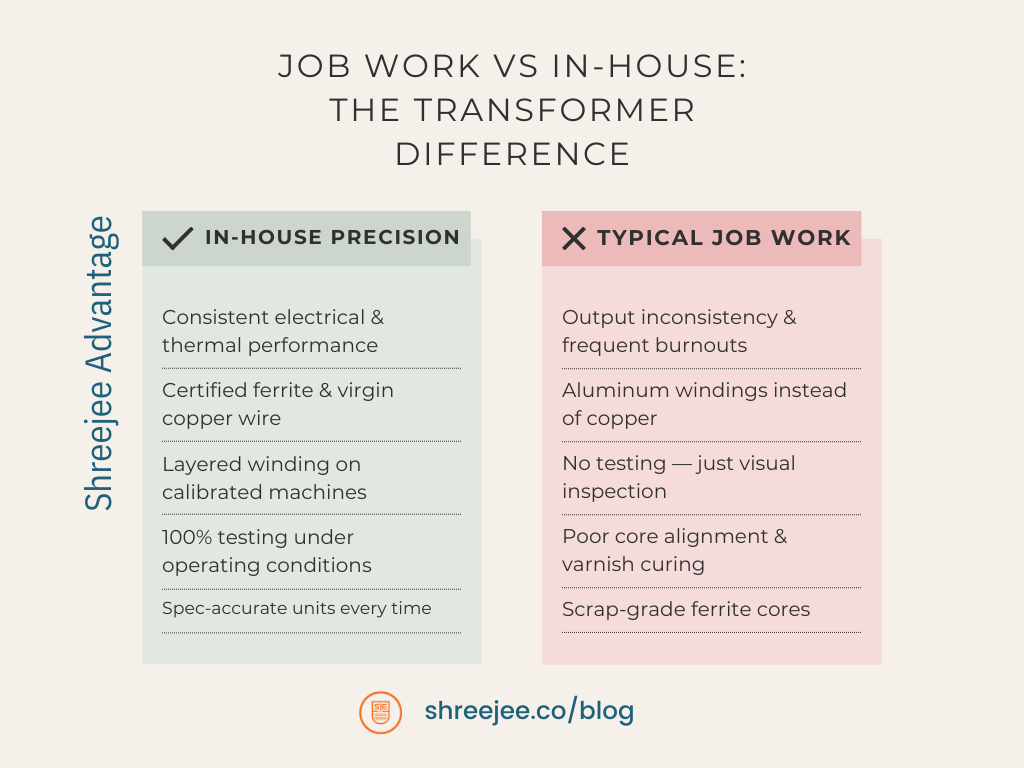
At Shreejee Electronics, we manufacture 100% in-house with complete control over raw materials, including:
- Certified ferrite cores
- High-grade enamelled copper wire
- Precision-controlled winding machines
- Standardized testing under simulated operating conditions
This ensures that every transformer we ship meets your exact specs, with no shortcuts, no surprises.
Want reliable performance and engineering accountability? Request a Quote from Shreejee Electronics and get a transformer you can trust.