An intense focus on quality is integral to any successful magnetics company’s corporate culture. In this blog post, we’ve outlined the key points of Quality Control (QC) and Quality Assurance (QA) strategies and how they can influence a magnetic company’s health, performance and output pricing.
Many customers believe that the transformer costs are limited to the upfront amount. At a basic level, transformer costs are determined by the time and materials used during the manufacturing process. However, transformer costs are impacted by numerous other complex factors as well, particularly when considering the impact on the overall system.
Magnetics contains several different raw materials, defects in the products that employ them are common. On average, an estimated 150 magnetic parts per million will fail. The accepted industry quality level is 125 defective parts per million. At Shreejee Electronics, we aim to do a lot better—our goal is zero defects on every product. Achieving this goal necessitates investing significant time and effort into quality assurance (QA).
Importance of Quality Assurance in Magnetics
QA is a proactive process that helps prevent production defects by optimizing the production process itself. It serves as a managerial tool used by design and planning teams. QA thus increases the final product quality levels achievable through carefully planned, implemented, and documented processes.
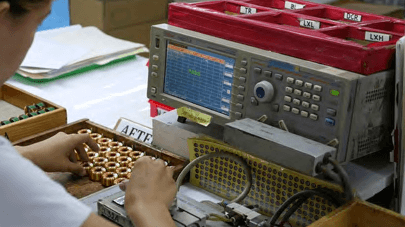
Some examples of QA activities include:
- Process mapping
- Supplier control
- Standards development
- Project audits
On the other hand, QC is a reactive process with a narrow focus, i.e., on the product being manufactured. The main objective of QC is to identify and correct defects in products at the time of their production. It is generally used as a corrective tool by the testing team.
Some examples of QA activities include:
- Inspection
- Testing
- Peer review
As both quality control and quality assurance ensure consistent parts that meet the required quality standards, they are imperative components of a company’s production operations.
Although many companies emphasize QC over QA, at Shreejee Electronics, we understand the importance of both processes. Great care is ensured, so our QC and QA teams are fully developed and prepared to maintain leading quality standards.
How Does QA Impact Cost?
QC alone does not always guarantee long-term reliability. The impact of QA on the cost of magnetics
is significant, as many factors contribute to the long-term effectiveness of the product employed.
Some of the factors that QA operations take into account are:
Component Failure
The reliability of a magnetics system as a whole is equivalent to the reliability of its components (e.g., transformers). If a single piece fails, it can result in damage to or failure of the entire system.
Excess heat generation
Transformers run hot if they employ improperly sized wire or cores with the incorrect shape, size, or construction material. In either case, the result is excess heat within the core.
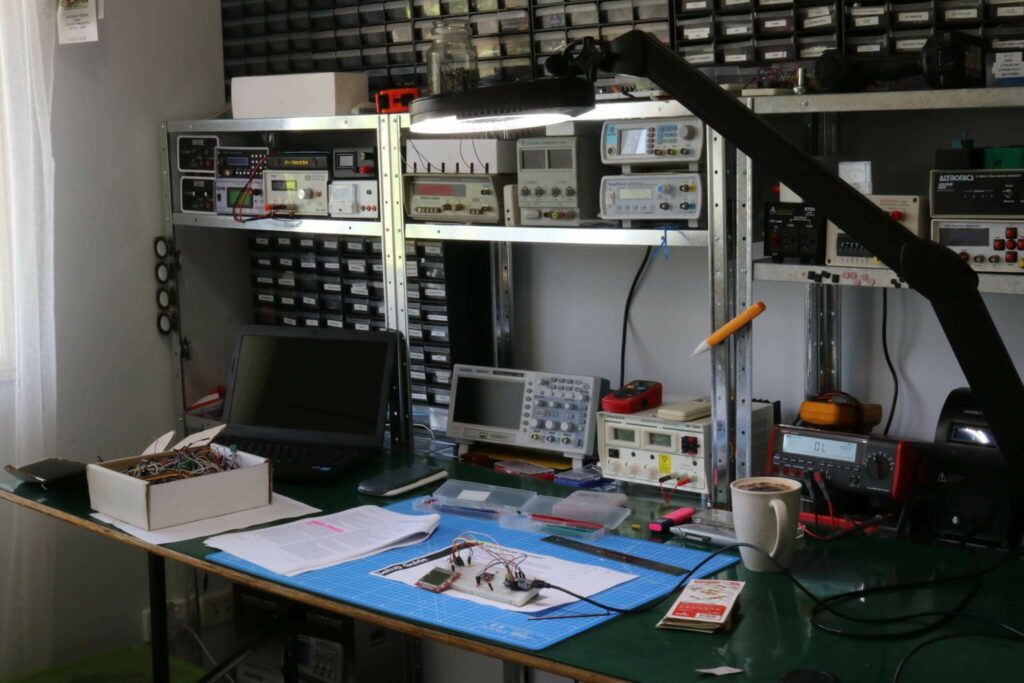
Production inconsistency
Suppose production operations demonstrate low accuracy levels from batch to batch. In that case, it is more likely that a customer may receive a part that only partially meets operating requirements and is more likely to fail.
Hard failure
This failure mode is characterized by a short between the primary and secondary sides of the transformer. It results from either a complete break-over—i.e., a shorting of high or sustained voltage between the primary and secondary through the insulation material—or a break in the winding due to high voltage.
Partial discharge
This failure mode results from ionization within the transformer, causing a small section of the insulation failure. When this occurs, it results in intermittent failures and shortened service life for the component.
Capacitive discharge
Capacitive discharge is one of the most challenging failure modes to identify as it exhibits system components failing without any apparent cause. Although outside of a connected circuit, the transformer appears fully functional; once a dynamic load is added, the system fails.
Transformer manufacturers well-versed in QA can prevent these common mistakes. On the customer end, purchasing a transformer from a company dedicated to QA helps lower overall costs by minimizing the need for repair and replacements—and the resulting downtime—throughout the product’s service life.
By partnering with us, our customers don’t need to sacrifice quality for efficiency or effectiveness—our company-wide focus on quality enables us to deliver highly dependable magnetics products.
To experience Shreejee Electronics’ quality for yourself and all the time and money savings that come with it, get in touch with our team today. We’d be happy to address any questions about quality or talk specifics about your proposed project.