In this post we’ll provide brief introduction to different types of wires available for numerous magnetic applications:
Round Wire
Round wire is the most commonly used wire, made of a round conducting section covered by an insulation layer
The applications of enameled wires are widespread, serving as components for electromagnetic products, including building generators, motors, transformers, inductors, relays, measuring instruments, control, telecommunication equipment, and other electronic equipment.
Depending upon the underlying application, they are available in many insulation types, such as polyester, polyurethane, polyester-amideimide and many gauges.
Litz Wire
Wire made of many thin wire strands, individually insulated and woven together in prescribed patterns.
Its ease of use and excellent AC resistance at high frequencies make them well suited for high-frequency transformers. Perhaps the most significant advantage that Litz wire can offer over any alternative is the reduction of AC losses due to the skin effect. They also help in achieving the least inductance leakage possible. However, as compared to round wire, they are pretty expensive.
Square Wire
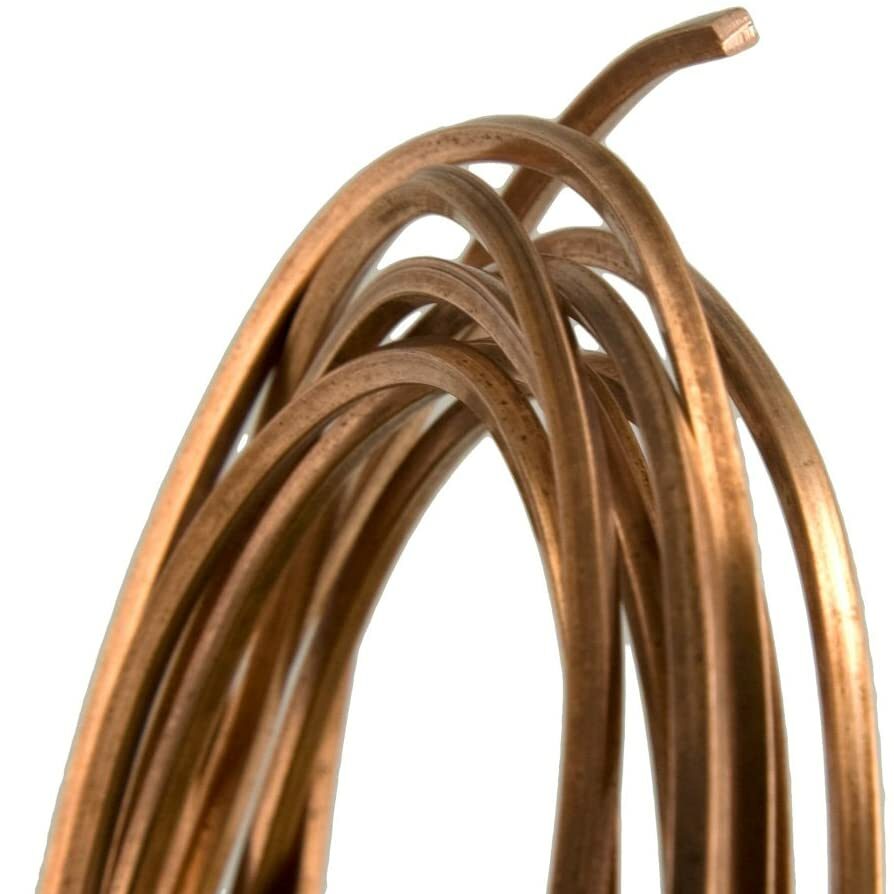
These are similar to the round wire but have a square section. Square wire has good compacity due to its large conducting section.
Paper-covered square wire has good mechanical properties and heat resistance and has been well received by local and international markets.
However, they have a very low AC resistance at high frequency, and fabrication cost is relatively high.
Rectangular Wire
The application of paper-covered rectangular wire is a type of conductor used for winding coils of transformers, welding machines, generators, and other electrical equipment. As such, these are similar to the round wire but have a rectangular section. It has good compacity due to its large conducting section.
Like square wire, they have a terrible AC resistance at high frequency and can be difficult to wind.
Foil Wire
Copper foil inductors also offer several practical benefits for engineers and manufacturers. These include the following advantages:
- Size reduction – Windings made from copper foil optimize space.
- Temperature control – Copper foil dissipates heat more effectively than magnet wire.
- Reduced voltage stress – Copper foil facilitates a reduction in voltage stresses between the turns in the winding.
- More robust – Foil-wound components offer increased mechanical strength compared to wire-wound components
- Cost-effective – Copper foil is much more affordable than Litz wire.
Planar Wire

Planar wires printed directly on a PCB, using external and internal layers when a low profile magnetic is needed. Manufacturers either use flat copper sheets or etch spiral patterns on a printed circuit board to form the “windings” of a planar transformer, replacing the turns of wire used to make other types.
Some planar transformers are commercially sold as discrete components. Other planar transformers are etched directly into the main printed circuit board and only need a ferrite core to be attached over the PCB. A planar transformer can be thinner than other transformers, which is helpful for low-profile applications or when several printed circuit boards are stacked. Almost all planar transformers use a planar ferrite core.
There are billions of possible combinations along the path towards designing the optimum magnetic element. When, additionally, different types of wires are introduced to the equation, the complexity of the problem can grow mind-numbingly large, mainly because the usage boundaries and their trade-offs are not always clear.
At Shreejee Electronics, our team of expert engineers can assist you with the selection process, ensuring that you get the suitable materials for your design.